一、層壓過程中的起泡和失壓現象:
造成原因:
1、壓機預壓力偏低。
2、溫度過高而且預壓停留時間太長。
3、PP樹脂的動態粘度高,熱壓時間太遲。
4、樹脂的流動性差或預壓力不足。
5、揮發物含量偏高
解決方法:
1、提高預壓力。
2、降溫、提高預壓力或縮短預壓周期。
3、應對照程式,時間,壓力,溫度,之間的關系
4、使壓力,溫度和流動性三者互相協調。
5、或降低揮發物含量。
二、壓合后基材發白和玻纖布紋線外觀明顯:
造成原因:
1、PP片樹脂流動度過高。
2、壓機預壓壓力偏高。
3、PP片中的樹脂含量低,固化時間較長。
4、熱壓時機把握不正確。
解決方法:
1、降低溫度或壓力。
2、降低壓機預壓力。
3、調整預壓力、溫度、熱壓的起始時間。
三、壓合后分層:
造成原因:
1、內層芯料板面油污污染。
2、PP片吸濕。
3、內層芯料吸濕。
4、內層芯料棕化不良。
5、PP和芯料的經緯向不一致。
6、內層芯料棕化后放置時間過長。
解決方法:
1、要求操作員必須戴防油污手套作業。
2、檢查PP存放環境,壓合前烘烤。
3、檢查PP存放環境,壓合前烘烤。
4、檢驗料棕化藥水濃度,棕化時間,清洗、烘干是否潔凈。
5、排版使PP和芯料的經緯向一致。
6、排版前,重新過棕化。
四、壓合后板翹現象:
造成原因:
1、非對稱性匹配壓合結構和走線方式。
2、混用不同廠商的不同規格的PP片。
3、PP樹脂膠固化時間不夠。
4、PP樹脂膠固化后,冷壓處置不當。
解決方法:
1、盡量設計對稱性壓合結構和走線方式。
2、同批次板必須使用同廠商、同規格的PP片作業。
3、必須保證PP樹脂膠固化時間周期。
4、按照程式、樹脂膠固化后正常冷壓。
五、壓合后板面凹痕
造成原因:
1、鋼板表面有膠跡、雜物。
2、PP片表面有附著物。
3、作業臺面清潔不夠
解決方法:
1、鋼板表面打磨光滑平整、無油污。
2、PP裁切后注意表面沒有雜物附著。
3、加強作業臺面清潔頻率。
六、多層板VIA孔無銅:
造成原因:
1、孔內毛刺較大。
2、孔壁粗糙。
3、板電氣泡導致的孔無銅。
4、干膜封孔不良導致的孔無銅。
5、孔壁油污導致的孔無銅。
解決方法:
1、除膠渣、用全新鉆咀。
2、用全新鉆咀,調節鉆機下鉆速度。
3、降低化學鍍銅液表面張力,減少孔內氣泡的形成,打氣均勻。
4、CAM盡量做大有銅孔的孔環,檢查干膜和銅面的附著力。
5、檢驗或更換酸性除油劑。
-
印制電路板
+關注
關注
14文章
957瀏覽量
40945 -
電路板
+關注
關注
140文章
4997瀏覽量
98878
發布評論請先 登錄
相關推薦
滬電股份43億投建AI芯片配套高端印制電路板項目
撓性電路板和柔性多層電路板區別
PCB電路板的阻抗工藝中控制要點
PCB多層板是什么?它有哪些特點?
如何檢測電路板上的元件
電路板檢修方法的優缺點有哪些
X-ray射線無損檢測設備檢測印制電路板
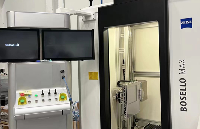
PCB設計中的常見問題有哪些?
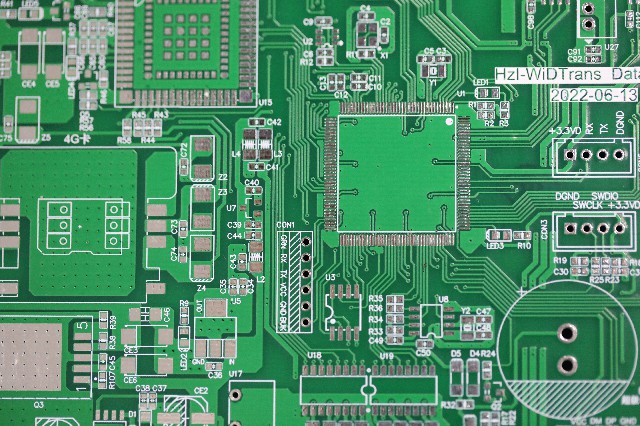
評論